The electromagnetic dry powder magnetic separator may encounter various
malfunctions during operation. The following are detailed descriptions of some
common faults and their solutions:
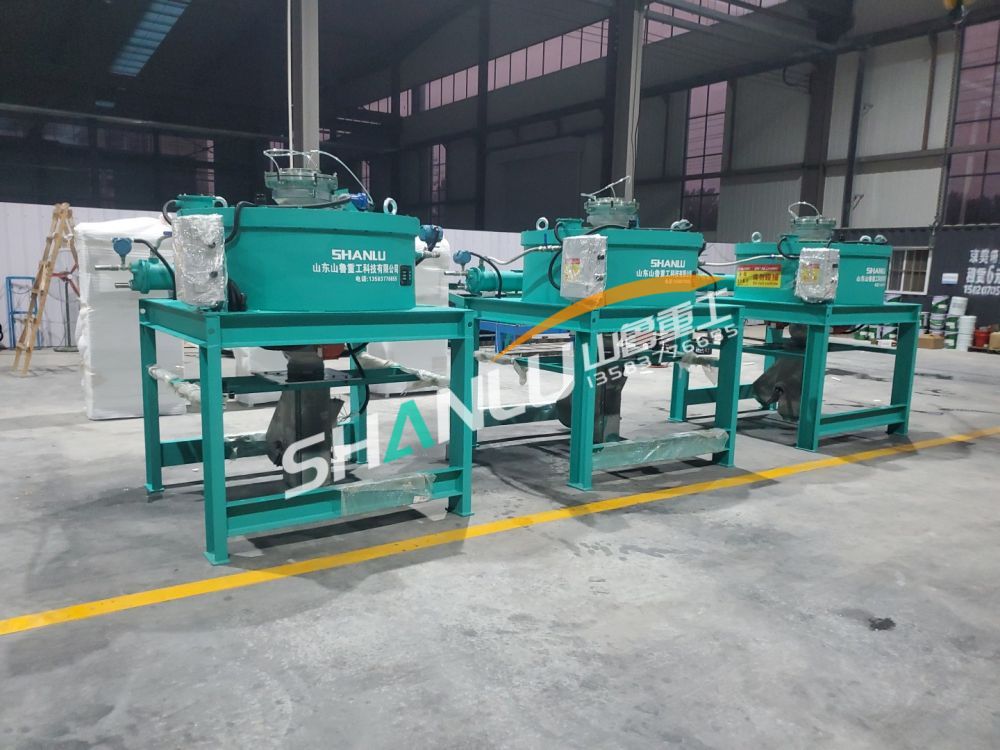
1. Abnormal magnetic field strength
Fault phenomenon
-Low magnetic field strength: Poor sorting effect, magnetic minerals cannot
be effectively adsorbed.
-High magnetic field strength: equipment overheating, increased energy
consumption, and adsorption of non-magnetic materials.
resolvent
-Check the power supply voltage: Ensure that the power supply voltage is
stable and meets the equipment requirements. If the voltage is unstable, a
voltage regulator needs to be configured.
-Detecting magnetic coil: Use a multimeter to measure the resistance value of
the magnetic coil, ensuring that there is no open or short circuit in the coil.
If there is damage, the magnetic coil needs to be replaced.
-Adjust current: Adjust the current setting of the equipment according to the
sorting requirements to ensure that the magnetic field strength is within a
reasonable range.
2. Uneven feeding
Fault phenomenon
-Excessive feeding: Material accumulation, decreased sorting efficiency, and
increased equipment load.
-Insufficient feed: low equipment processing capacity and resource waste.
resolvent
-Check the feeding equipment: Ensure that the vibrating feeder or belt feeder
is operating normally, and adjust the feeding speed.
-Uniform feeding: Maintain continuous and uniform feeding during operation to
avoid feeding in large quantities at once.
-Adjust the height of the silo: Adjust the height of the silo and the size of
the outlet to control the material flow rate.
3. Magnetic medium blockage
Fault phenomenon
-Magnetic medium blockage: Materials cannot pass through the magnetic
separation zone smoothly, resulting in a decrease in sorting efficiency.
-Magnetic medium wear: The surface of the magnetic medium is rough, and the
sorting effect decreases.
resolvent
-Regular cleaning of magnetic media: Regularly clean the accumulated
substances and impurities on the surface of the magnetic media to maintain its
smoothness.
-Replace magnetic media: Regularly replace worn or aged magnetic media
according to usage.
-Optimize the layout of magnetic media: Adjust the layout of magnetic media
to make it more reasonable and reduce the probability of blockage.
4. High temperature
Fault phenomenon
-Equipment overheating: Excessive temperature can cause protective shutdown
or damage to the equipment.
-Reduced sorting efficiency: Excessive temperature affects magnetic field
strength and sorting efficiency.
resolvent
-Check the cooling system: Ensure that the cooling system is working
properly, clean the dust on the radiator and fan.
-Control environmental temperature: In high temperature environments,
increase ventilation and cooling measures to maintain a suitable temperature for
equipment operation.
-Adjust working hours: Reasonably arrange the working time and downtime of
equipment to prevent overheating caused by prolonged continuous operation.
5. Electrical malfunction
Fault phenomenon
-Control system malfunction: The equipment cannot start or stop normally, and
the control system is unresponsive.
-Damage to electrical components: Failure of electrical components such as
contactors and relays.
resolvent
-Check the electrical circuit: Check whether the connection of the electrical
circuit is normal, whether there is looseness or disconnection, and repair it in
a timely manner.
-Detecting electrical components: Use a multimeter to check the working
status of electrical components and replace damaged ones.
-Upgrade the control system: Consider upgrading or updating the aging control
system and adopting more advanced electrical control technology.
6. Transmission system malfunction
Fault phenomenon
-Transmission belt slippage: The belt becomes loose or worn, resulting in a
decrease in transmission efficiency.
-Bearing wear: Poor operation or abnormal noise of bearings, increased
equipment vibration.
resolvent
-Adjust or replace the belt: Regularly check the tightness of the drive belt
and adjust or replace it if necessary.
-Lubricating bearings: Regularly add lubricating oil to bearings to maintain
good lubrication and reduce wear.
-Replace bearings: If the bearings are severely worn, they should be replaced
with new bearings in a timely manner to ensure smooth operation of the
equipment.
7. Abnormal equipment vibration or noise
Fault phenomenon
-Equipment vibration: Abnormal vibration occurs during equipment operation,
which affects stability and sorting efficiency.
-Increased noise: Equipment operation noise increases, which may be due to
mechanical component wear or looseness.
resolvent
-Check fasteners: Regularly inspect the fasteners of various parts of the
equipment for looseness and tighten them if necessary.
-Check the transmission system: Check the gears, chains, and belts of the
transmission system to ensure that there is no wear or looseness.
-Adjust balance: Check the balance status of the equipment and make
adjustments if necessary to ensure smooth operation of the equipment.
8. Improper operation
Fault phenomenon
-Misoperation: Improper operation leading to equipment malfunction or
damage.
-Parameter setting error: The device parameter settings are unreasonable,
affecting the sorting effect.
resolvent
-Operation training: Provide systematic training to operators to ensure they
are familiar with the operating procedures and maintenance methods of the
equipment.
-Standardized operation: Develop standardized operating procedures, strictly
follow the procedures for operation, and avoid misoperation.
-Parameter optimization: Based on the actual production situation, set the
operating parameters of the equipment reasonably to ensure the best sorting
effect.
conclusion
The common faults and solutions of electromagnetic dry powder magnetic
separators cover various aspects of equipment operation. By regular inspection,
reasonable maintenance, scientific operation, and timely handling of faults, the
stability and sorting efficiency of equipment can be effectively improved,
ensuring the continuity and efficiency of production.