Permanent magnet wet flat magnetic separator is a magnetic separation
equipment commonly used in mineral processing, metallurgy, chemical industry and
other fields, widely used to remove magnetic impurities from ores or other
materials. It uses permanent magnets to generate a stable magnetic field and
sorts materials through wet processing (using water as a medium), which has the
advantages of high efficiency, environmental protection, and low energy
consumption.
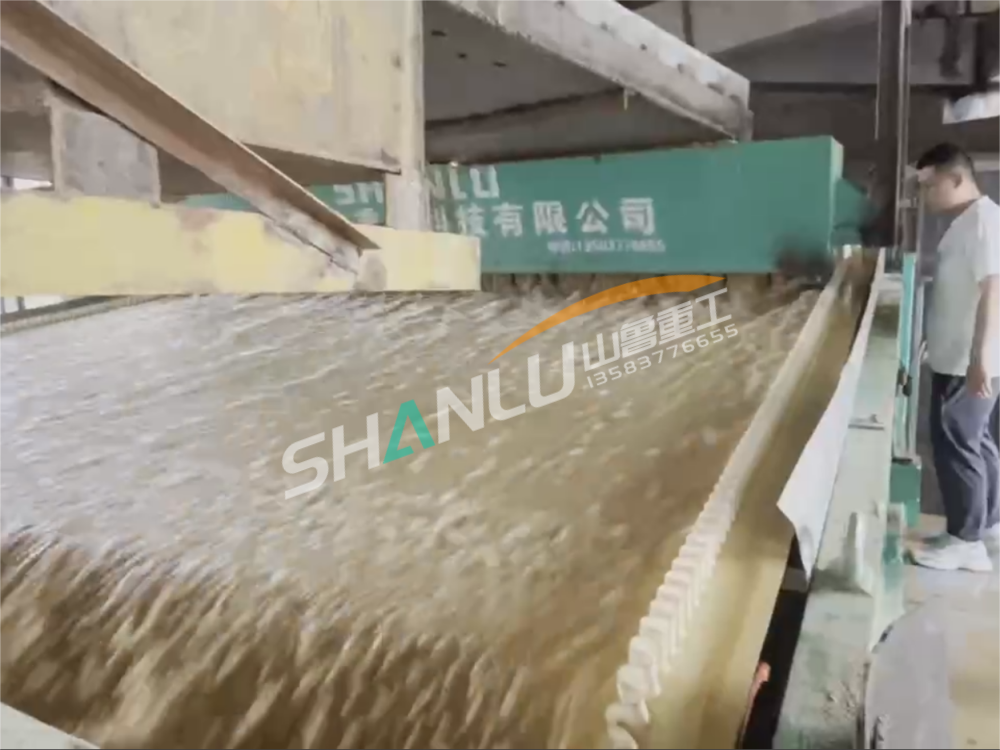
main features
Permanent magnet source: The permanent magnet wet flat magnetic separator
uses permanent magnet materials as the magnetic source, usually high-strength
magnetic materials such as neodymium iron boron (NdFeB). Compared with
electromagnetic magnetic separators, permanent magnet equipment does not require
external power supply, reducing energy consumption and maintenance costs.
Flat structure: The magnetic separation surface of this device is usually a
flat plate-like structure with uniform magnetic field effect. Flat design is
beneficial for the contact between materials and magnetic fields, improving
sorting efficiency.
Wet sorting: Wet sorting is the process of mixing materials with water to
suspend them in a water flow. Magnetic substances are adsorbed onto the magnetic
plates of the magnetic separator, while non-magnetic substances are discharged
with the water flow.
High efficiency and low energy consumption: The permanent magnet wet flat
magnetic separator achieves efficient separation with its stable magnetic field
and simple working principle, and has low energy consumption.
working principle
The working principle of the permanent magnet wet flat plate magnetic
separator mainly relies on the magnetic field's attraction to the magnetic
minerals in the material for separation. The specific process is as follows:
Material feeding: Ore, sand, gravel or other materials are fed into the feed
inlet of the magnetic separator through the feeding system with water. The
material is fully dispersed by water flow to form a suspension.
Sorting process: When the material in the suspension flows through a flat
magnetic field, magnetic substances will be adsorbed by the strong magnetic
field on the magnetic separation plate, while non-magnetic substances will be
carried away with the water flow.
Discharge of magnetic materials: After sorting, the magnetic materials are
adsorbed onto the magnetic separation plate, and are adsorbed and directionally
moved by the magnetic field on the surface of the plate, and finally discharged
through the discharge port.
Discharge of non-magnetic materials: Non magnetic materials will be carried
away by water flow and discharged outside the equipment. Usually, non-magnetic
materials are directed to another discharge outlet or further processed through
sedimentation tanks.
Main applications
Mineral sorting: Permanent magnet wet flat magnetic separators are widely
used in ore sorting, especially in removing iron impurities from iron ores,
titanium ores, and bauxite ores to remove harmful substances.
Quartz sand production: Iron impurities in quartz sand can be removed by a
permanent magnet wet plate magnetic separator, thereby improving the purity of
quartz sand and meeting the requirements of high-purity materials in glass
manufacturing, semiconductor industry, and other industries.
Coal processing: During the coal washing process, magnetic separators are
used to remove iron mineral impurities from coal and improve coal quality.
Non metallic minerals such as sodium feldspar, bauxite, tantalum niobium ore,
etc. can be effectively treated for iron removal using a permanent magnet wet
plate magnetic separator to remove magnetic impurities from these ores.
Chemical industry: used for impurity sorting in chemical raw materials, such
as quartz sand treatment in ceramic and glass production processes.
Equipment structure
The structure of a permanent magnet wet flat magnetic separator includes the
following main parts:
Permanent magnet source: A magnet typically composed of a series of permanent
magnet materials (such as neodymium iron boron magnets) that provide a stable
and powerful magnetic field. The magnetic field is generally arranged on or
below the flat plate.
Magnetic separator: The magnetic separator is the working surface of the
equipment, usually in the shape of a flat plate, made of corrosion-resistant
materials such as stainless steel, with magnetic materials arranged on the
surface, in direct contact with the material.
Feeding device: responsible for mixing materials and water and feeding them
into the magnetic separator. The design of the feed inlet can usually adjust the
water flow rate and material flow rate to ensure the best sorting effect.
Water flow system: used to guide water flow, ensure uniform dispersion of
materials on the magnetic separator, and effectively remove non-magnetic
impurities. The design of the water flow system is crucial as it directly
affects the sorting efficiency.
Unloading device: used to discharge magnetic substances adsorbed by a
magnetic field from the magnetic separator. Unloading is usually accomplished
through mechanical or gravity methods.
Slag discharge system: used to collect and discharge non-magnetic substances,
ensuring the expected accuracy of material sorting.
advantage
High energy efficiency and low energy consumption: Compared with
electromagnetic magnetic separators, permanent magnet wet flat magnetic
separators do not require external power sources, resulting in lower energy
consumption and lower operating costs.
Environmental Protection: Adopting wet separation method can effectively
reduce dust pollution and is more environmentally friendly than dry magnetic
separation.
Efficient sorting: The permanent magnet wet flat magnetic separator can
provide a stable magnetic field, enabling efficient sorting of magnetic
materials and improving production efficiency.
Strong adaptability: Suitable for various types of minerals and materials,
especially for processing ores, sands, coal, and non-metallic minerals.
Low maintenance cost: Due to the use of permanent magnet sources, the
operating cost of this equipment is relatively low, and the magnetic field is
stable, reducing the maintenance requirements of the equipment.
Common problems and solutions
The sorting effect is not ideal:
Solution: Check if the feed quantity, particle size, concentration, etc. meet
the requirements. Adjust the water flow rate, feeding speed, and magnetic field
strength to ensure the best magnetic separation effect.
Wear of magnetic separator plate:
Solution: Regularly check the wear of the magnetic separation plate,
especially when handling hard materials. Need to replace the severely worn
magnetic separator to maintain the magnetic separation effect.
Uneven water flow:
Solution: Check if the water flow system is blocked, adjust the pressure of
the water pump to ensure even water flow and sufficient dispersion of
materials.
Equipment malfunction or jamming:
Solution: Check if there are any foreign objects stuck in the equipment,
clean the equipment regularly, and avoid impurities in the materials blocking
the normal operation of the equipment.
summary
The permanent magnet wet flat magnetic separator is an efficient and
environmentally friendly sorting equipment that utilizes strong magnetic fields
and wet processing methods to effectively remove magnetic impurities from
minerals and materials. It is widely used in the sorting and purification of
quartz sand, ore, coal, non-metallic minerals, etc. It has the advantages of
energy saving, low maintenance, and high efficiency, and is an important
equipment in modern mineral processing and material handling.