What is a drum screen?
Drum screen is a widely used screening equipment in industries such as
mining, chemical, and building materials, used to separate different particle
sizes in materials. Its main working principle is to roll the material along the
surface of the sieve through the rotation of the drum, thereby achieving graded
screening of the material. It can efficiently screen materials of various
particle sizes, especially suitable for materials with larger particles and
irregular shapes.
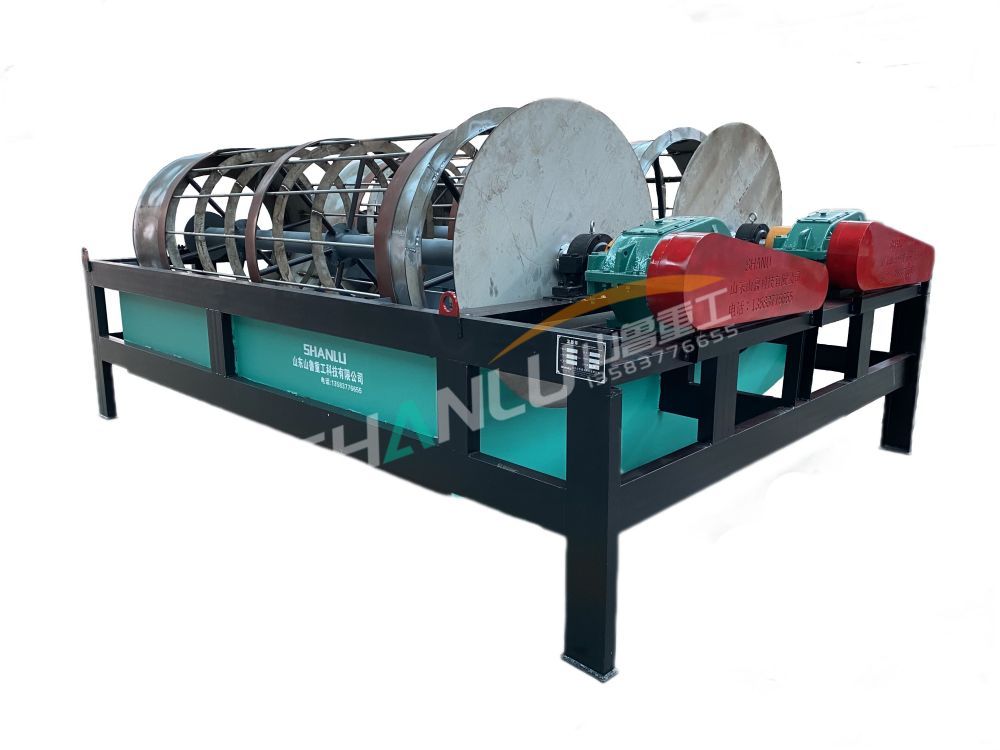
1、 Working principle of drum screen
The drum screen is usually composed of a rotating cylindrical sieve mesh, and
the material enters the drum through the feeding port. As the drum rotates, the
material will roll on the surface of the screen and be separated through screens
of different apertures. Larger particles will be blocked by the sieve and
discharged from the discharge port, while smaller particles will fall through
the pores of the sieve and enter the lower collection area.
Material entry: The material is fed into the rotating drum screen through the
feeding port.
Screening process: The rotation of the drum screen causes the material to
move along the screen surface, with larger particles intercepted by the sieve
and smaller particles passing through the pores of the sieve.
Classification and separation: Through the rotation of the drum, materials
are divided into different grades according to particle size and discharged from
multiple discharge ports.
2、 The main components of a drum screen
Screen cylinder:
The sieve cylinder is the core part of the drum sieve, usually made of mesh
screen or mesh plate, with a certain aperture. The rotational motion of the
sieve cylinder is the basis for material screening.
Motor and reducer:
The motor provides power for the drum screen, while the reducer is used to
slow down and increase the speed of the screen cylinder. Usually, the motor and
reducer are connected together to control the rotation of the drum.
transmission:
Including motors, reducers, chains or belts, responsible for transmitting the
power of the motor to the sieve cylinder to rotate it.
Supporting structure:
The drum screen is usually fixed on the ground by a support frame to ensure
stable rotation of the screen cylinder.
Discharge outlet:
The drum screen is equipped with multiple discharge ports according to the
particle size of the material, which respectively discharge materials of
different particle levels.
Feed inlet:
The material enters the screening cylinder through the feeding port, usually
at one end of the screening cylinder.
Drive system:
Composed of a motor and a transmission device, it provides the power for the
rotation of the screen cylinder.
3、 The main types of drum screens
Cylindrical sieve:
It is the most common type, and the sieve is cylindrical in shape, suitable
for screening materials of various particle sizes.
Diagonal sieve:
The sieve tube is inclined at an angle and can use gravity to help materials
pass through the sieve. It is usually suitable for larger particle
materials.
Vibration drum screen:
On the basis of traditional drum screens, vibration devices have been
installed to enhance the screening efficiency of materials, suitable for wet and
viscous materials.
Mobile drum screen:
Suitable for occasions where frequent changes of work locations are required,
usually supported by wheels or tracks for easy mobility.
4、 Application fields of drum screen
Mining:
In the screening process of raw materials such as ores, coal, and metal ores,
drum screens can effectively separate minerals of different particle sizes.
Especially suitable for screening coarse minerals or wet ores.
Building materials industry:
In scenarios such as sand and gravel sorting, stone screening, and concrete
sand and gravel screening, drum screens are commonly used to separate building
materials such as sand and stone with different particle sizes.
Fertilizer industry:
In fertilizer production, drum screens are used for grading and screening raw
materials and finished products to improve product quality and production
efficiency.
Chemical industry:
The drum screen provides an efficient solution for screening chemical raw
materials, especially in the sorting of fine-grained materials.
Recycling industry:
In the process of waste recycling, drum screens can help separate waste of
different particle sizes, especially for the classification and treatment of
metals, plastics, paper, etc.
Agriculture:
Used for screening agricultural products (such as grains, seeds, etc.) to
ensure the purity and quality of the final product.
Food processing:
Used for screening food raw materials, helping to remove impurities and
improve product quality.
5、 Advantages and disadvantages of drum screen
advantage:
High screening efficiency:
The drum screen is suitable for processing large particle materials and can
quickly complete screening, making it suitable for large-scale production.
Simple structure and easy maintenance:
Due to its simple structure, the drum screen is easy to maintain and repair,
and has a long service life.
Strong adaptability:
The drum screen can handle different types of materials, including dry and
wet materials.
Uniform screening:
The drum screen can evenly grade materials through rotation and gravity,
avoiding the problem of uneven screening.
Continuous work:
The drum screen can achieve continuous operation, improving the automation
level of the production line.
Disadvantages:
Large footprint:
Roller screens are usually quite large and require a large area for
installation and operation.
Limited processing granularity:
For very small particle materials, the screening effect of the drum screen is
poor.
High energy consumption:
The drum screen needs to be driven by an electric motor to rotate the screen
cylinder, so the energy consumption is high, especially in large-scale
production.
Material blockage issue:
If there is too much wet material or viscous substance in the material, it is
easy to cause screen blockage and affect production efficiency.
6、 Maintenance and upkeep
Regular maintenance and upkeep are crucial to ensure the long-term efficient
operation of the drum screen. The main maintenance measures include:
Regularly clean the sieve mesh:
The screen mesh of the drum screen is prone to material accumulation, and
regular cleaning of the screen mesh can maintain screening efficiency.
Check the drive system:
Regularly inspect drive components such as motors, reducers, chains, etc. to
ensure their normal operation.
Check the sieve cylinder:
The sieve cylinder is prone to wear or deformation during use, and its
integrity should be checked regularly.
Lubricate various components:
Regularly lubricate the moving parts of the drum screen to reduce wear and
extend the service life of the equipment.
Check the discharge and feed ports:
Ensure smooth entry and exit of materials to avoid blockages that may affect
production efficiency.
7、 Summary
Drum screen is a screening equipment widely used in industries such as
mining, building materials, and chemical engineering, with advantages such as
high efficiency, simplicity, and strong adaptability. It can efficiently
classify and screen materials of various particle sizes, suitable for screening
tasks of large particles and wet materials. Through proper maintenance and
upkeep, the drum screen can operate efficiently for a long time, providing
stable support for various production processes.