How to achieve automation control in quartz sand production line?
The automation control of quartz sand production line can significantly
improve production efficiency, reduce labor costs, minimize operational errors,
and ensure the stability of product quality. Implementing automation control not
only involves the selection of hardware devices, but also the integration and
optimization of software systems. The following are the main steps and technical
means to achieve automation control in the quartz sand production line:
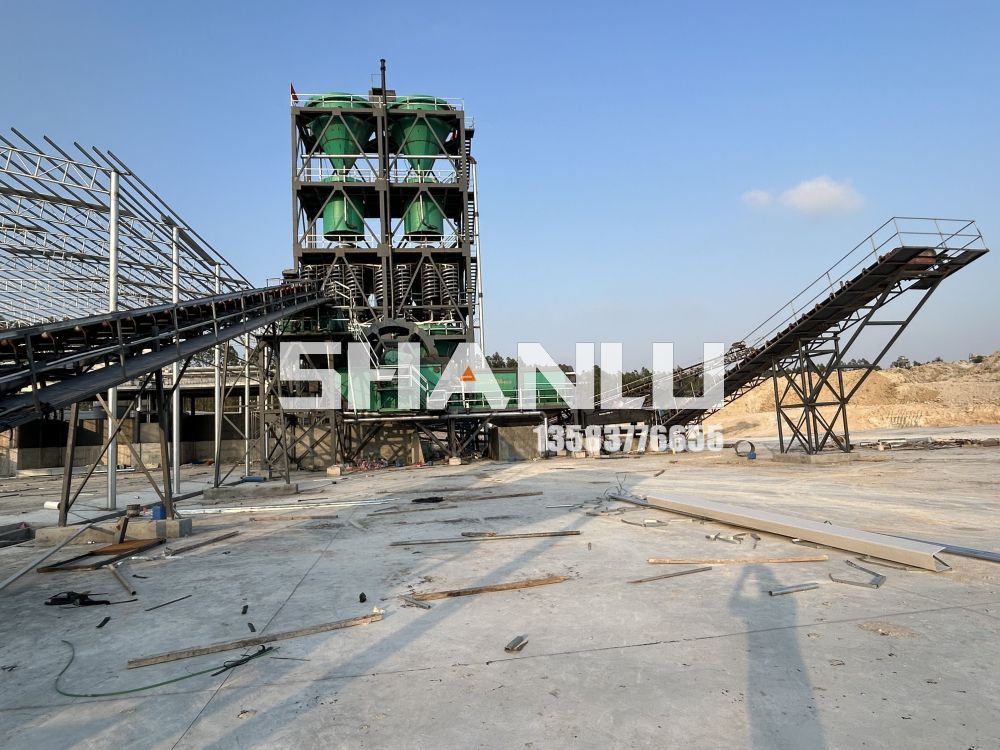
1. Objectives and advantages of automation control
1.1 Objectives
Improve production efficiency: The automation control system can ensure that
the production line operates efficiently by optimizing equipment scheduling and
workflow, reducing downtime and the occurrence of failures.
Ensure stable product quality: Automated control can monitor various
parameters in real-time during the production process, such as temperature,
humidity, particle size, etc., to ensure consistency in product quality.
Reduce labor costs: Through automation control, reliance on manual operations
can be reduced, reducing labor costs and the possibility of operational
errors.
Improve safety: Automation systems can remotely control and monitor hazardous
equipment in the production line in real-time, reducing the risk of on-site
exposure for operators.
1.2 Advantages
Real time monitoring and data analysis: The system can collect various types
of data in the production process in real time and optimize and adjust them
through data analysis.
Precise adjustment and dynamic adjustment: The automation system can
dynamically adjust various production parameters according to production needs,
ensuring the optimal state of the production process.
Energy conservation and emission reduction: Through intelligent control
systems, energy use can be optimized and unnecessary energy waste can be
reduced.
2. Core components of automation control system
2.1 Sensors and Detection Systems
The core of an automation system is sensors and detection equipment, which
are used to collect real-time data from various aspects of the production line,
including:
Material flow sensor: used to monitor the inflow, outflow, and transmission
speed of materials.
Particle size analyzer: Real time monitoring of the size and uniformity of
sand particles.
Humidity sensor: monitors the moisture content of quartz sand, especially in
wet production processes.
Temperature sensor: controls the temperature of the working environment of
the equipment, especially during the calcination and drying processes, which
require strict temperature control.
Vibration sensor: used to monitor the working status of screening equipment,
crushers, etc., to ensure the normal operation of the equipment.
2.2 Automation Control System (PLC/DCS)
PLC (Programmable Logic Controller): PLC is the "brain" of automation control
systems, responsible for controlling and coordinating various equipment
throughout the production process. By controlling the switch, speed, and running
time of various devices through PLC, the smooth operation of the production line
is ensured.
DCS (Distributed Control System): Suitable for large-scale quartz sand
production lines, DCS can more accurately control the operation of each unit in
the entire production process, and achieve distributed control and adjustment
through real-time data transmission.
SCADA system: The SCADA (Supervisory Control and Data Acquisition) system
works in conjunction with PLC and DCS systems to provide real-time monitoring of
production process data, helping operators view equipment status, alarm
information, and production process diagrams.
2.3 Variable frequency drive and electric actuator
Variable frequency drive (VFD): By adjusting the speed of the equipment
through the VFD, precise control of equipment such as crushers, grinders, and
vibrating screens can be achieved, avoiding overload operation and reducing
energy consumption.
Electric actuator: used for automatic control of feeding system, discharging
system, airflow control, etc., achieving precise operation through electric
actuators to ensure smooth production process.
3. Implementation steps of automation control for quartz sand production
line
3.1 System Planning and Design
Firstly, it is necessary to design a suitable automation control system based
on the actual situation of the quartz sand production line. This includes:
Assess the automation requirements for each stage, such as crushing,
screening, grinding, drying, etc.
Choose appropriate sensors and automatic control equipment.
Determine the configuration and communication architecture of control systems
such as PLC and DCS.
3.2 Selection of Automation Equipment
Choosing suitable automation equipment is crucial for improving production
efficiency:
Equipment such as crushers, grinders, screening machines, and dryers must be
compatible with the automation control system and support remote control.
Automated conveying system: The transportation and stacking of quartz sand
rely on automated conveyor belts, equipped with automatic start/stop devices,
speed control, and other functions.
3.3 System Integration and Debugging
After the equipment selection and system design are completed, carry out
system integration and debugging work to ensure the collaborative work between
all equipment, sensors, actuators, and control systems:
Data collection and analysis: By integrating sensors, real-time production
data is obtained and uploaded to the control system for analysis and
optimization.
Automatic parameter adjustment: Real time adjustment of parameters such as
particle size, humidity, temperature, etc., to ensure stable operation of the
production line.
3.4 Human Machine Interface (HMI) and Remote Monitoring
HMI (Human Machine Interface): Through HMI, operators can view real-time data
of the production process and make manual interventions or adjustments.
Remote monitoring system: Through cloud platforms and remote monitoring
systems, operators can monitor the status of the production line anytime and
anywhere, and promptly handle faults and adjust parameters.
4. Optimization and maintenance of automation control
4.1 Data driven optimization and adjustment
Automated systems can optimize production processes by collecting large
amounts of production data for big data analysis and prediction
Intelligent scheduling: Based on real-time data from the production line, the
automation system can optimize production scheduling, adjust the operating
status of various equipment, and avoid excessive load or idling.
Predictive maintenance: By monitoring the operational status of equipment,
the system can predict potential failures in advance, perform repairs or replace
components in advance, and avoid production downtime.
4.2 Equipment Fault Diagnosis and Alarm
The automation control system is equipped with real-time fault diagnosis and
alarm functions, which can detect abnormal situations of equipment (such as
motor overheating, screen blockage, etc.), trigger alarms in a timely manner,
and take measures to reduce the risk of equipment damage.
4.3 Regular calibration and maintenance
Automated systems require regular calibration and maintenance:
Sensor calibration: Ensure the measurement accuracy of all sensors, such as
regular calibration of temperature, humidity, and particle size sensors.
Control system update: Update the software of PLC and DCS systems to ensure
stable operation of the system.
5. Typical case analysis
Case 1: Automated Control of Wet Quartz Sand Production Line
In the wet production line, the moisture content of quartz sand is monitored
in real-time by sensors, and the PLC system adjusts the temperature and humidity
of the dryer based on the data to ensure that the dryness of the sand particles
meets the requirements. At the same time, the screening process of the vibrating
screen is also controlled by an automated system to ensure uniform particle
distribution and avoid excessive screening.
Case 2: Automation Control of Quartz Sand Crusher
The quartz sand crusher dynamically adjusts the speed and load of the crusher
through a frequency conversion speed control system, avoiding equipment overload
and improving production efficiency. The PLC system automatically adjusts the
working parameters of the crusher based on material characteristics and performs
real-time monitoring.
summarize
The automation control of quartz sand production line is an important means
to improve efficiency, reduce energy consumption, and ensure product quality in
modern production. Through the combination of sensors, PLC systems, automatic
adjustment equipment and other technical means, efficient and stable production
control can be achieved. At the same time, the introduction of data analysis and
remote monitoring systems has made the production process more intelligent,
reduced manual intervention, and improved the overall operational efficiency and
reliability of the production line.