The automation control of quartz sand production line is a complex and
delicate project, involving the integration and optimization of multiple
equipment and process links. Automated control can improve production
efficiency, reduce labor costs, enhance product quality, and ensure the
stability of the production process. The following is a detailed explanation for
achieving automation control of quartz sand production line:
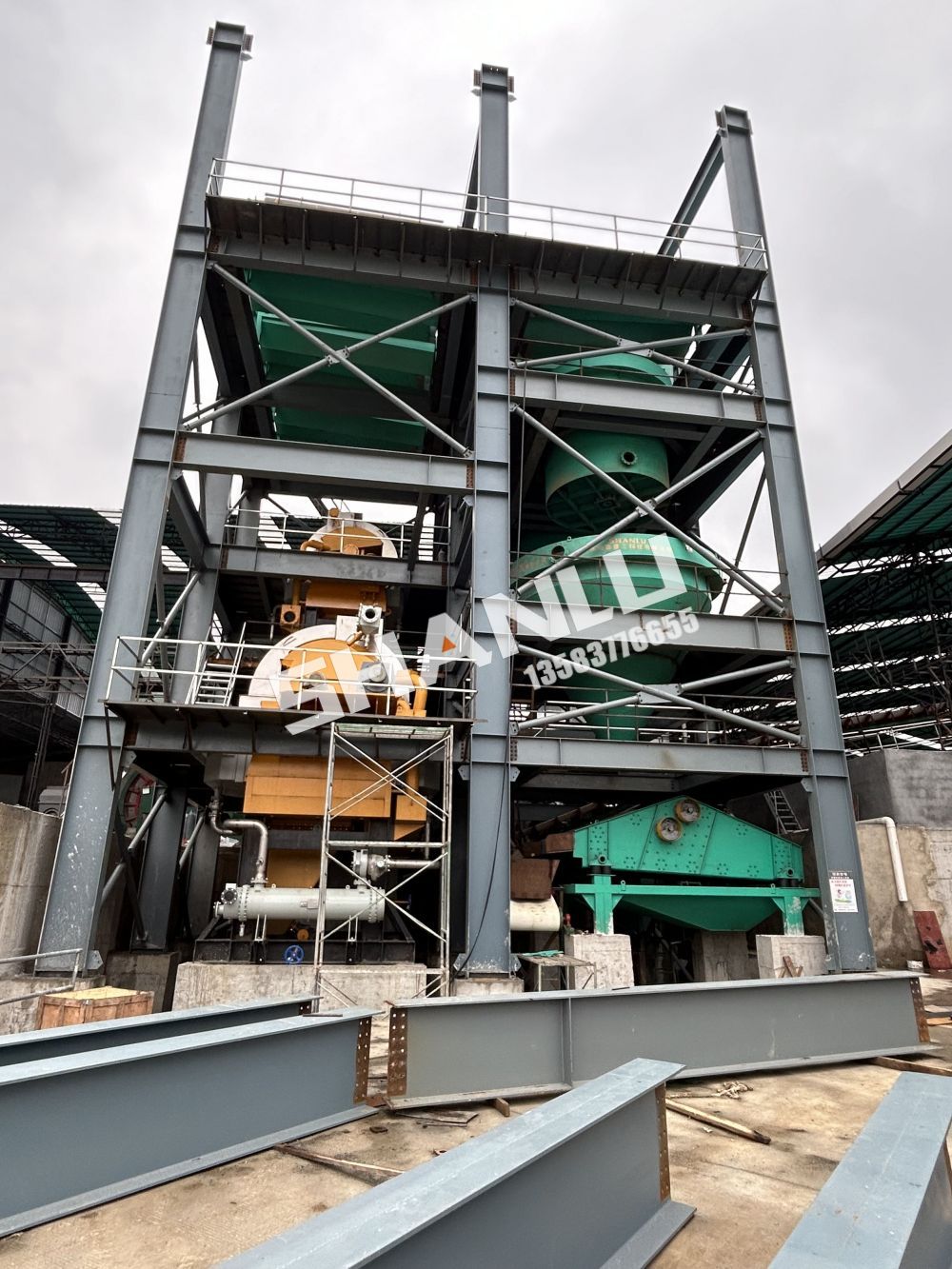
1. Selection and architecture of control system
-PLC control system: The programmable logic controller (PLC) is the core of
the automation of the quartz sand production line, which can centrally control
and manage the entire production process. The PLC system achieves automatic
start stop, parameter adjustment, and fault detection of equipment by writing
control programs.
-Distributed Control System (DCS): For large-scale quartz sand production
lines, a distributed control system (DCS) can be used to distribute multiple PLC
control modules in different production stages, and data exchange and
coordinated control are carried out between each module through a communication
network.
-SCADA system: Supervisory Control and Data Acquisition System (SCADA) is
used for real-time monitoring of the production process, displaying equipment
status, process parameters, and alarm information through the Human Machine
Interface (HMI). Operators can remotely control the production line from the
central control room.
2. Automation control of key equipment
-Crushing equipment: The automation control of the crusher mainly includes
controlling the feeding amount, monitoring the operating status of the
equipment, and automatically adjusting the discharge particle size. Sensors
monitor the load situation of the equipment, and the PLC system adjusts the
feeding speed according to the load situation to avoid equipment overload.
-Grinding machine: The automation control of the grinding machine is mainly
achieved by controlling the motor speed, the amount of grinding medium added,
and the grinding time. The PLC system can automatically adjust equipment
parameters based on real-time detection of grinding effect, ensuring the best
grinding effect.
-Vibration screen: The automation control of vibration screen includes the
adjustment of screening frequency and amplitude. By monitoring the screening
effect and particle size distribution of materials through sensors, the PLC
system automatically adjusts the working parameters of the vibrating screen to
improve screening efficiency and accuracy.
-Magnetic separator: The automation control of the magnetic separator is
mainly reflected in the adjustment of magnetic field strength, the control of
feed rate, and the adjustment of discharge speed. By detecting the sorting
effect online, the PLC system can automatically optimize the operating
parameters of the magnetic separator.
3. Automation of material conveying system
-Automatic control of conveyor belt: The conveyor belt is an important
component of the quartz sand production line, and its automation control mainly
includes adjusting the conveying speed and controlling the material flow rate.
The PLC system automatically adjusts the speed of the conveyor belt based on the
processing capacity of each device, ensuring uniform distribution and continuous
conveying of materials.
-Bucket elevator and screw conveyor: The automation control of these
conveying equipment includes start stop control, speed regulation, and material
blockage detection. Sensors detect the flow status of materials, and the PLC
system automatically adjusts the operating status of the conveying equipment
based on the material flow rate.
4. Automation of water treatment systems
-Water quality monitoring and control: The automated water treatment system
monitors parameters such as suspended solids, pH value, and salt content in the
water through an online water quality analyzer. The PLC system automatically
adjusts the dosage of chemicals, drainage volume, and circulating water volume
based on changes in water quality to ensure that production water meets process
requirements.
-Mud treatment and recovery: The concentration and discharge of mud can be
managed through an automated control system, which can automatically adjust the
operating parameters of the dewatering equipment to achieve effective treatment
and recovery of mud.
5. Environmental monitoring and control
-Dust control system: The automated dust control system monitors the
concentration of dust in the air in real time through dust sensors installed in
various production processes. The PLC system automatically starts the dust
removal equipment based on the monitoring data to ensure that the production
environment meets environmental protection requirements.
-Wastewater treatment and discharge: The automated wastewater treatment
system monitors the discharge volume and pollutant content of wastewater in real
time, automatically adjusts the operating parameters of wastewater treatment
equipment, and ensures that wastewater discharge meets environmental
standards.
6. Real time monitoring and data analysis of the production process
-Real time monitoring: The SCADA system can monitor the operation status,
process parameters, and equipment status of each link in the production line in
real time. Operators can view and control the entire production process through
the HMI interface in the central control room.
-Data collection and analysis: Automated systems can collect and store
various types of data during the production process, including equipment
operating parameters, production efficiency, product quality data, etc. Through
data analysis, process parameters can be optimized to improve production
efficiency and product quality.
7. Fault detection and alarm system
-Online fault detection: The automation system uses sensors and monitoring
devices to detect the real-time operating status of equipment, such as
temperature, pressure, current, and other parameters. If any abnormality is
found, the system will automatically record and send an alarm message.
-Automatic alarm and shutdown protection: When a device malfunction or
abnormal situation is detected, the automation system will issue an audible and
visual alarm and automatically shut down or switch to a safe mode according to a
preset program to prevent equipment damage or production accidents.
8. Production Planning and Scheduling Management
-Automated production planning: Through the integration of ERP system and
production automation system, production plans can be automatically issued to
the production line. The system automatically arranges production tasks,
schedules equipment and materials based on order requirements and production
capacity, ensuring timely completion of production tasks.
-Production process optimization: Through real-time monitoring and data
analysis, automation systems can optimize and adjust the production process,
such as adjusting equipment operating parameters, optimizing material flow
paths, etc., to improve production efficiency and resource utilization.
9. Human computer collaboration and remote control
-Human machine collaboration: The automation control system works closely
with operators, and through the HMI interface, operators can easily monitor and
operate the production line. The system can automatically adjust equipment
parameters according to production needs, reducing manual intervention.
-Remote monitoring and control: through the Internet and Internet of Things
technology, managers can monitor and control the production line remotely, view
production status, adjust production parameters, and even deal with fault and
alarm information.
10. Safety and Emergency Management
-Automated safety system: Safety sensors and emergency devices are integrated
with the automation control system. In the event of an emergency, the system
automatically triggers safety programs such as shutting down, cutting off power,
and starting emergency equipment to ensure the safety of personnel and
equipment.
-Emergency response and recovery: Automated systems can record and analyze
the causes of emergency events and provide recovery recommendations to help
operators quickly resume production.
Through the above measures, the automation control of the quartz sand
production line can significantly improve production efficiency, reduce
operating costs, and ensure product quality and consistency. In addition,
automation systems can reduce the complexity of manual operations, improve
production safety and controllability, and make production line operations more
stable and efficient.