Improving the separation accuracy of electromagnetic dry powder magnetic
separators is a key step in optimizing mineral processing, which directly
affects the quality and purity of the final product. The following are detailed
strategies and methods for improving the sorting accuracy of electromagnetic dry
powder magnetic separators:
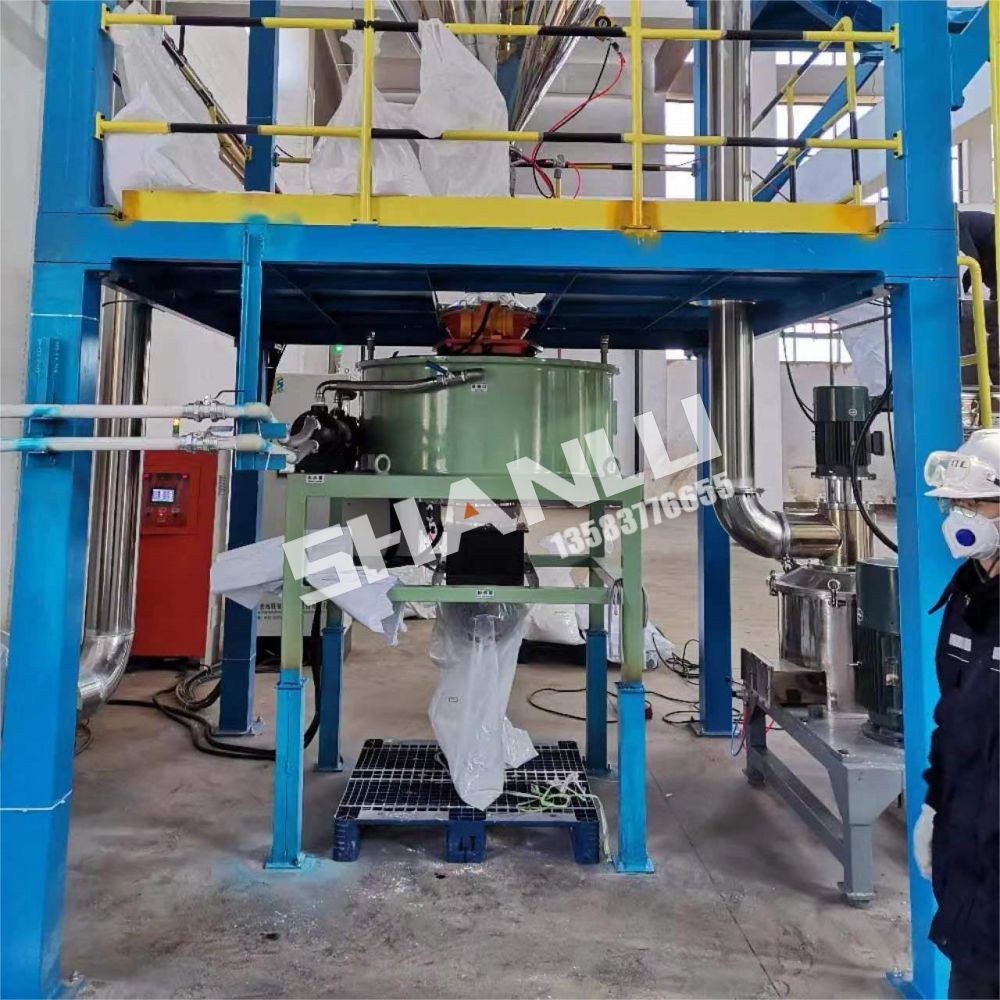
1. Optimize magnetic field strength and distribution
-Magnetic field strength adjustment: The magnetic field strength directly
affects the separation effect of magnetic and non-magnetic materials. By
adjusting the current of the electromagnetic coil, the magnetic field strength
can be changed to ensure that magnetic materials receive sufficient magnetic
force in the magnetic field, while non-magnetic materials are not affected.
-Uniform magnetic field distribution: The uniformity of magnetic field
distribution is crucial in the sorting area. The uniform distribution of
magnetic field can be ensured by improving the design of electromagnetic coils
or using a multi-level magnetic field layout to avoid the occurrence of "blind
spots" or excessively strong local magnetic fields, which can lead to a decrease
in sorting accuracy.
2. Reasonably design the structure of the magnetic separator
-Magnetic separator speed adjustment: The speed of the magnetic separator
affects the residence time of the material in the magnetic field. By adjusting
the speed reasonably, the magnetic material has sufficient time to be subjected
to the magnetic field and adsorbed, thereby improving the sorting accuracy.
Usually, slower speeds help improve accuracy, but production efficiency may
decrease, so a balance needs to be found between accuracy and efficiency.
-The design of sorting area: The length and width of the sorting area
directly affect the effectiveness of the sorting process. By designing the
sorting area reasonably, it is possible to ensure that materials are fully
exposed to the magnetic field, thereby improving the recovery rate and purity of
magnetic materials.
3. Optimization of material properties
-Material particle size control: The particle size of materials has a
significant impact on sorting accuracy. The sorting effect of materials with
excessively large or small particles is poor, so it is necessary to use
screening or grinding processes before entering the magnetic separator to ensure
that the material particle size is uniform and suitable for the sorting capacity
of the magnetic separator.
-Humidity and flowability of materials: The humidity of materials can affect
their flowability during magnetic separation. Dry materials have better fluidity
and higher sorting accuracy. Therefore, before the material enters the magnetic
separator, its humidity needs to be controlled to ensure good fluidity of the
material.
4. Feeding method and flow control
-Feed uniformity: The uniformity of the feed is crucial for the sorting
effect. By installing vibration feeders or other feeding devices, ensure that
materials enter the magnetic separator uniformly and continuously, avoiding a
decrease in sorting accuracy caused by uneven feeding.
-Feed speed and flow control: Controlling the feed speed and flow rate can
ensure uniform distribution of materials in the magnetic field. A too fast feed
rate may result in insufficient residence time of the material in the magnetic
field, while a too slow feed rate may reduce processing capacity. Therefore, it
is necessary to adjust the feeding speed and flow rate according to production
requirements and equipment capacity.
5. Use of auxiliary equipment
-Iron remover: Before the material enters the magnetic separator, using an
iron remover can first remove large pieces of strong magnetic impurities, reduce
the burden on the magnetic separator, and improve the accuracy of the subsequent
sorting process.
-Multi stage magnetic separation: By using a multi-stage magnetic separation
process, the products sorted once are sorted again, which can effectively
improve the purity and sorting accuracy of the products. The magnetic field
strength and other parameters of each magnetic separation can be adjusted
according to the properties of the material.
6. Fine tuning of magnetic separator parameters
-Adjusting current and voltage: By finely adjusting the current and voltage
of the electromagnetic coil, the strength and stability of the magnetic field
can be controlled, thereby improving sorting accuracy. Suggest conducting
experiments based on material characteristics to determine the optimal current
and voltage settings.
-Optimizing the position of the magnetic system: Adjusting the position of
the magnetic system can affect the direction and magnitude of the force on the
material in the magnetic field. By adjusting the position of the magnetic
system, magnetic materials can be more easily adsorbed onto the magnetic
separator, improving sorting efficiency and accuracy.
7. Real time monitoring and adjustment
-Online detection system: Install an online detection system to monitor in
real-time the material characteristics, magnetic field strength, equipment
operation status, etc. during the sorting process, which can timely detect and
correct problems in sorting and improve sorting accuracy.
-Automated control system: Through the automated control system, various
parameters of the magnetic separator are adjusted in real time, such as magnetic
field strength, feed speed, etc., to ensure that the sorting process is always
in the best state.
8. Equipment maintenance and upkeep
-Regular cleaning: The magnetic medium inside the magnetic separator is prone
to adsorbing small magnetic particles, which affects the sorting accuracy.
Therefore, it is very important to regularly clean the impurities and iron
filings accumulated inside the magnetic separator, maintain the cleanliness of
the magnetic separator, and improve the sorting accuracy.
-Equipment maintenance and upkeep: Regularly inspect the magnetic separator
to ensure that the equipment is in good condition and avoid sorting accuracy
issues caused by equipment failure or performance degradation.
9. Experimental research and optimization
-Small scale and pilot scale studies: Before large-scale production, conduct
small scale and pilot scale studies to determine the optimal sorting parameters
and process flow through experiments. Based on the experimental results,
optimize the operating parameters and production process of the magnetic
separator.
-Process optimization and upgrading: Based on the actual production
situation, continuously optimize and upgrade the magnetic separation process,
such as using more advanced magnetic separation technology or equipment to
improve separation accuracy.
10. Control of environmental factors
-Temperature and humidity control: Environmental temperature and humidity
have a certain impact on the electrical components and magnetic field stability
of the magnetic separator. Control the temperature and humidity of the working
environment to avoid the impact of extreme conditions on equipment performance
and ensure sorting accuracy.
Through the above measures, the sorting accuracy of the electromagnetic dry
powder magnetic separator can be effectively improved, thereby enhancing the
effectiveness of mineral processing and meeting the production requirements of
high-purity and high-quality products. These measures need to be selected and
applied in conjunction with specific production situations and material
characteristics to achieve optimal results.