The design and implementation of quality inspection processes are crucial in
quartz sand production lines, as they directly affect the product's
qualification rate and market competitiveness. Through a series of quality
inspection processes and control measures, it can be ensured that the produced
quartz sand meets the specifications and quality requirements. The following is
a detailed explanation of the quality inspection process in the quartz sand
production line and how it ensures product qualification rate:
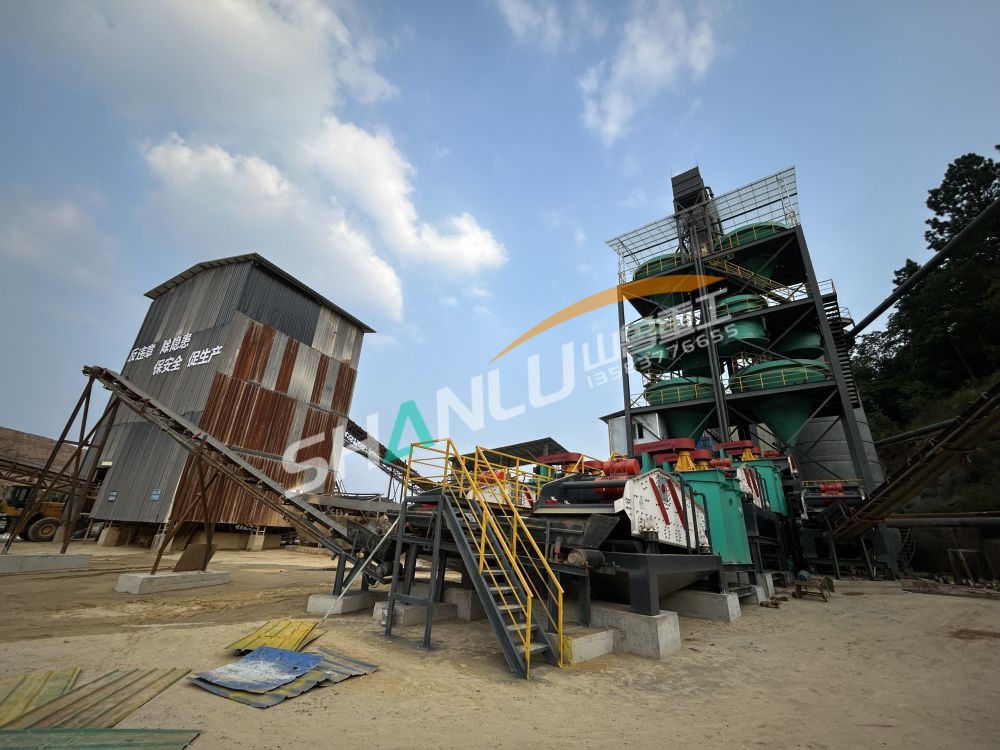
1. Raw material inspection
-Raw material screening and acceptance: Before the production of quartz sand
begins, strict screening and acceptance of raw materials are carried out,
including checking the purity, color, hardness, and particle size of quartz
stone. Ensure that the raw materials used meet production requirements through
physical testing and chemical analysis.
-Impurity detection and removal: Through preliminary screening and magnetic
separation, impurities such as iron, clay, and other minerals in the raw
materials are detected and removed. The quality control in this stage ensures
the purity of the product in the subsequent production process.
2. Online detection during the production process
-Particle size monitoring: In the crushing and sanding process, an online
particle size analyzer is installed to monitor the particle size distribution of
quartz sand in real time, ensuring that the particles generated during the
production process meet the predetermined standards. If any deviation is found,
automatically adjust the operating parameters of the crusher or sanding
machine.
-Magnetic substance content monitoring: Online magnetic substance detection
equipment is used to monitor the iron content in quartz sand, ensuring that the
magnetic separation process effectively removes iron impurities. If the iron
content exceeds the standard, the system will trigger an alarm and automatically
adjust the working status of the magnetic separator.
-Concentration and purity analysis: During wet or dry sorting processes,
online concentration meters and purity analyzers are used to detect the
concentration and purity of quartz sand in the slurry to ensure compliance with
production standards.
3. Periodic testing of intermediate products
-Sample collection: After each key production process is completed,
intermediate product samples are collected for laboratory analysis, such as at
various stages after sanding, magnetic separation, and screening. Detect the
particle size, purity, and other physical and chemical properties of quartz sand
through regular and random sampling.
-Testing standards: The testing results of each stage are compared with the
predetermined quality standards to ensure that the semi-finished products output
from each production process meet the requirements. If any non-compliance with
the standards is found, adjust the process parameters or rework in a timely
manner.
4. Finished product testing
-Particle size distribution analysis: By screening testing or laser particle
size analyzer, the particle size distribution of the finished quartz sand is
detected to ensure that the particle size distribution of the product is within
the range required by the customer.
-Chemical composition analysis: Conduct chemical composition testing on the
finished quartz sand, especially the content of silicon dioxide (SiO2) and other
impurities. Ensure that the chemical composition meets the standards through
X-ray fluorescence spectroscopy (XRF) or other chemical analysis methods.
-Physical property testing: Testing the physical properties of quartz sand,
such as hardness, wear resistance, specific gravity, and color, to ensure
compliance with industry standards and customer requirements.
5. Pre packaging inspection
-Impurity detection: Before packaging, the final impurity detection is
carried out on the finished product to ensure that there are no visible foreign
impurities and pollutants. Use automatic detection equipment or manual visual
inspection to remove non-conforming products.
-Weight and packaging inspection: Weigh and seal the finished product
packaging to ensure accurate weight of each bag (or barrel) and secure packaging
that can maintain product quality during transportation.
6. Laboratory testing and certification
-Laboratory testing: Regularly send the produced quartz sand samples to the
laboratory for comprehensive testing, including high-precision physical and
chemical testing. The laboratory test results can further verify the accuracy of
online and phased testing.
-Third party testing and certification: In order to ensure that the product
meets industry standards or special customer requirements, product samples can
be sent to third-party testing institutions for certification to obtain
corresponding quality certification certificates and enhance the product's
market competitiveness.
7. Data recording and analysis
-Quality data recording: All quality inspection data generated during the
production process are recorded, including raw material testing results, online
testing data, and finished product testing results for each batch. Establish
quality records to provide a basis for subsequent quality traceability and
problem analysis.
-Data analysis and improvement: By analyzing quality data, identify weak
links and potential problems in the production process, and propose improvement
measures. Continuously optimize production processes and quality inspection
procedures to improve product qualification rates and consistency.
8. Feedback and Adjustment
-Customer feedback mechanism: Establish a customer feedback mechanism to
collect quality issues encountered by customers during use, and incorporate
feedback information into the quality management system. Based on customer
feedback, adjust production and quality inspection processes in a timely manner
to improve product quality.
-Internal Quality Improvement Meeting: Regularly hold quality analysis and
improvement meetings, summarize problems discovered during production and
quality inspection processes, develop targeted solutions, and promote continuous
improvement.
9. Training and Management
-Quality control personnel training: Regularly train quality control
personnel to ensure they are familiar with the latest testing standards,
operating procedures, and quality management requirements. Improving the
professional competence and sense of responsibility of quality inspection
personnel is the key to ensuring the effectiveness of the quality inspection
process.
-Production management and supervision: Strengthen production management and
supervision, ensure that process operators strictly follow production
procedures, and avoid product quality problems caused by operational errors or
management negligence.
10. Establishment and Certification of Quality Management System
-ISO Quality Management System: Establish and implement the ISO 9001 quality
management system to systematically manage the production and quality inspection
processes. By obtaining ISO certification, we ensure the standardization and
normalization of the production process, and enhance the stability of product
quality.
-Continuous improvement mechanism: The quality management system should
include a continuous improvement mechanism, which ensures the continuous
optimization of the quality inspection process and improves the product
qualification rate through regular internal audits, management reviews, and
quality improvement measures.
Through the above quality inspection process, the quartz sand production line
can effectively control product quality, ensuring product qualification rate and
consistency. The implementation of these processes not only helps meet customer
needs, but also reduces production costs, minimizes quality losses, and enhances
the market competitiveness of the enterprise.