The main production process of quartz sand
The production process of quartz sand mainly varies depending on the source
and use of raw materials, but usually includes the following main steps:
crushing, screening, sand washing, magnetic separation, flotation, and drying.
The following is a detailed description of common processes in quartz sand
production:
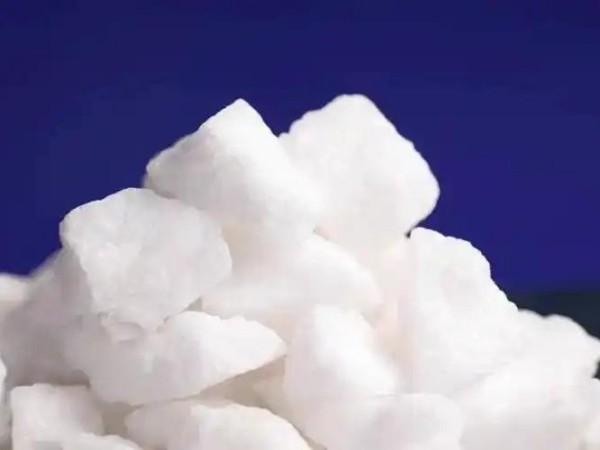
1. Raw material preparation
Raw material selection: The main raw material for quartz sand is natural
quartz ore or quartzite. Require high content of silicon dioxide (SiO ₂) and low
impurities in the raw materials.
Preliminary crushing: The raw materials are initially crushed using a jaw
crusher or hammer crusher to reduce the particle size of the stones and
facilitate subsequent processing.
2. Crushing and Grinding
Medium fine crushing: Use a cone crusher or impact crusher to further crush
the raw material into the desired particle size.
Rod mill or ball mill: Fine grind the crushed quartz stone to achieve the
desired fineness.
Wet grinding: Adding moisture to the grinding process to form a slurry can
reduce dust and improve grinding efficiency.
Dry grinding: suitable for applications that are sensitive to moisture.
3. Screening
Vibration screening: Quartz sand is divided into different particle sizes
through a vibration screen to ensure that the product meets application
requirements.
Separate coarse and fine particles for different purposes.
Materials that do not meet the standards are returned to the crushing or
grinding process.
4. Sand washing
Sand washing machine cleaning: Remove impurities such as soil and dust on the
surface of quartz sand through water washing to improve the purity of quartz
sand.
Use a spiral sand washing machine or a wheel bucket sand washing machine for
cleaning.
This stage is particularly important for producing high-purity quartz
sand.
5. Magnetic Separation
Electromagnetic or permanent magnet magnetic separator: removes magnetic
impurities such as iron minerals and other metal impurities from quartz
sand.
In the production of high-purity quartz sand, magnetic separation is carried
out multiple times to ensure extremely low impurity content.
Dry magnetic separation: suitable for dry quartz sand.
Wet magnetic separation: Combined with sand washing process, it has higher
efficiency.
6. Flotation
Flotation equipment: Separate impurities such as mica and feldspar in quartz
sand through chemical agents.
The flotation process is suitable for the production of high-purity quartz
sand and can effectively increase the SiO ₂ content.
Common medications include cationic or anionic collectors.
7. Acid washing
Chemical acid washing: Soak quartz sand in acid solution (such as
hydrochloric acid, hydrofluoric acid) to remove trace metal impurities (such as
iron, aluminum).
This process is suitable for the production of ultra-high purity quartz sand,
ensuring that it meets the needs of the electronics or photovoltaic
industries.
8. Drying
Drying equipment: Wet processed quartz sand is dried to the desired moisture
content using a drum dryer or hot air stove.
Some applications require quartz sand to be completely dry.
Dried quartz sand is easy to store and transport.
9. Packaging and Storage
Automatic packaging machine: Packaging the processed quartz sand according to
specifications, usually in bagged or bulk form.
Storage requirements: The storage environment needs to be moisture-proof to
ensure that the quality of quartz sand is not affected.
Common Process Flow Chart
Raw materials → preliminary crushing → medium fine crushing → grinding →
screening → sand washing → magnetic separation → flotation → acid washing →
drying → packaging and storage
Factors influencing the selection of production processes
Product Usage:
Glass industry: Need to control particle size and remove impurities.
Casting industry: emphasizing particle size uniformity and heat
resistance.
High purity quartz sand: requires high-precision processes such as multiple
magnetic separation and acid washing.
Raw material characteristics:
The hardness and iron content of the raw ore determine the crushing and
purification process.
Environmental requirements:
During the sand and acid washing processes, a water treatment system needs to
be installed to reduce the impact of emissions on the environment.