Choosing suitable quartz sand production equipment is crucial for improving
production efficiency, ensuring product quality, and reducing production costs.
Suitable equipment can effectively meet process requirements and improve the
overall performance of the production line. The following are the key factors
and suggestions to consider when choosing quartz sand production equipment:
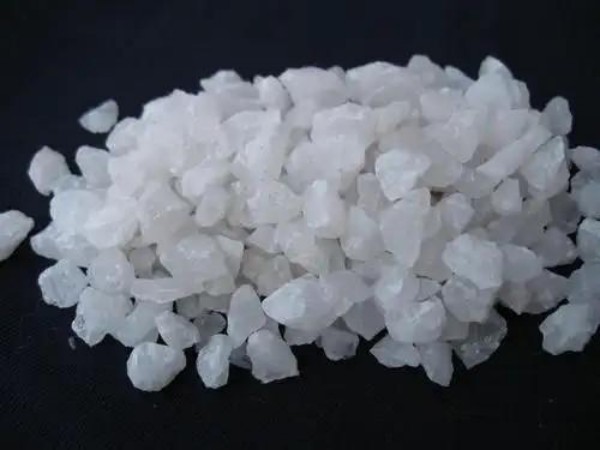
1. Select equipment based on the properties of raw materials
The raw material for quartz sand is usually natural quartz ore or quartzite,
and the different properties of the raw material (such as hardness, particle
size, impurities, etc.) determine what type of equipment needs to be selected.
Specifically, as follows:
Hardness: Quartz ore has a high hardness, so it is necessary to choose
equipment with high strength and wear resistance, such as sturdy crushers and
grinders.
Impurity content: When the content of impurities (such as iron, aluminum, and
soil) in the raw materials is high, equipment such as magnetic separators and
flotation machines need to be configured for impurity removal.
Particle size requirements: Select appropriate crushers, grinders, and
screening equipment based on the particle size requirements of the final
product. For example, if the product requires finer particle size, it may be
necessary to use a ball mill or rod mill for fine grinding.
2. Production scale and capacity requirements
The scale and production capacity of the production line are key factors in
selecting equipment. Production lines of different scales have different
requirements for equipment output.
Small scale production line: suitable for using small and flexible equipment,
such as small jaw crushers, vibrating screens, etc. These devices have a small
footprint and strong flexibility.
Large scale production line: requires equipment with high production
capacity, such as large cone crushers, large grinding machines, large magnetic
separators, etc., to ensure meeting the needs of large-scale production.
3. Optimization of process flow
The process flow of quartz sand production line includes crushing, grinding,
screening, sand washing, magnetic separation, flotation and other steps. When
selecting equipment, it is necessary to consider the process requirements of
each link and ensure the coordination between various devices:
Crushing equipment: Choose crushing equipment that is suitable for the
hardness and particle size requirements of the raw materials. Common equipment
includes jaw crushers, impact crushers, and cone crushers.
Grinding equipment: If further grinding of quartz ore is required, rod mills
or ball mills can be used. Rod mills are suitable for processing ores containing
more fine particles, while ball mills are suitable for processing finer
ores.
Screening equipment: Vibrating screens are usually used to screen ores into
different particle sizes, ensuring that suitable particles enter the next stage.
When choosing a vibrating screen, it is necessary to consider the selection of
screen aperture and screening efficiency.
Sand washing equipment: Sand washing machines such as spiral sand washing
machines and wheel bucket sand washing machines can remove impurities from
quartz sand, especially in wet production, which is very important.
Magnetic separation equipment: such as electromagnetic dry powder magnetic
separators and permanent magnet magnetic separators, used to remove
ferromagnetic impurities from quartz sand and ensure product purity.
Flotation equipment: used to remove small impurities, especially in the
production of high-purity quartz sand, flotation equipment can further improve
the purity of the product.
4. Equipment performance and technical parameters
When choosing equipment, in addition to considering production capacity and
scale, it is also necessary to pay attention to the technical performance and
parameters of the equipment. Mainly includes:
Energy efficiency: Choose equipment with high energy efficiency, such as
high-efficiency crushers and grinding machines, to reduce energy consumption
costs.
Stability of operation: Choose equipment with high stability and low failure
rate to ensure the continuity of the production line and reduce downtime.
Particle size adjustment range: Whether the equipment can easily adjust the
discharge particle size to meet the needs of different products.
Wear resistance and durability: In the production process of quartz sand,
equipment wear is significant. Choosing materials and designs with strong wear
resistance (such as high chromium alloys, hardening treatments, etc.) can
improve the service life of the equipment.
5. Environmental and energy-saving requirements
During the production process of quartz sand, a large amount of dust, noise,
and water pollution may be generated, so the environmental performance should be
considered when selecting equipment.
Dust control: Choose efficient dust removal devices such as bag filters and
wet dust removal systems to reduce dust pollution.
Noise control: Choose low-noise equipment, especially in the grinding
process, using silent design or installing sound insulation devices.
Water treatment system: Water is required in wet production, and equipment
with water treatment systems such as water circulation systems and wastewater
treatment devices should be selected to reduce water pollution.
6. Automation and Intelligence of Equipment
Modern quartz sand production lines are increasingly moving towards
automation and intelligence, and the level of equipment intelligence is crucial
for improving production efficiency and reducing labor costs.
Automated control system: Choosing equipment equipped with PLC control system
can achieve automatic adjustment, remote monitoring and other functions,
reducing manual intervention.
Intelligent sensors and data monitoring: The equipment is equipped with
intelligent sensors and data acquisition systems, which can monitor various data
during the production process in real time (such as temperature, humidity,
particle size, etc.), detect problems in a timely manner, and adjust equipment
operating parameters.
7. Equipment brand and supplier
When selecting equipment, in addition to technical parameters, the supplier's
brand, after-sales service, and equipment quality assurance should also be
considered:
Brand reputation: Choosing equipment from well-known brands usually results
in more reliable quality and guaranteed after-sales service.
After sales service: Confirm whether the supplier provides comprehensive
services such as equipment installation and commissioning, operation training,
maintenance, etc.
Equipment quality assurance: The quality assurance period of the equipment,
the supply of spare parts, and long-term maintenance support are key factors
that need to be considered when selecting a supplier.
8. Budget and Investment Return
When selecting equipment, it is necessary to comprehensively consider the
budget of the production line and the expected return on investment:
Budget constraints: Choose cost-effective equipment based on the budget to
avoid unnecessary economic pressure caused by excessive investment.
Return on investment: Evaluate the production efficiency, durability, and
energy consumption of equipment to ensure that equipment investment can bring
returns within a reasonable time.