Design points of mud sedimentation tank for quartz sand washing equipment
In the production process of quartz sand, water washing equipment is used to
remove soil, impurities, and other fine particles from the sand. The wastewater
after sand washing usually contains a large amount of mud, suspended solids, and
small particles. In order to avoid direct discharge of wastewater causing
pollution to the environment, it is necessary to use a mud sedimentation tank
for effective solid-liquid separation. The following are the key points for
designing a mud settling tank for quartz sand washing equipment:
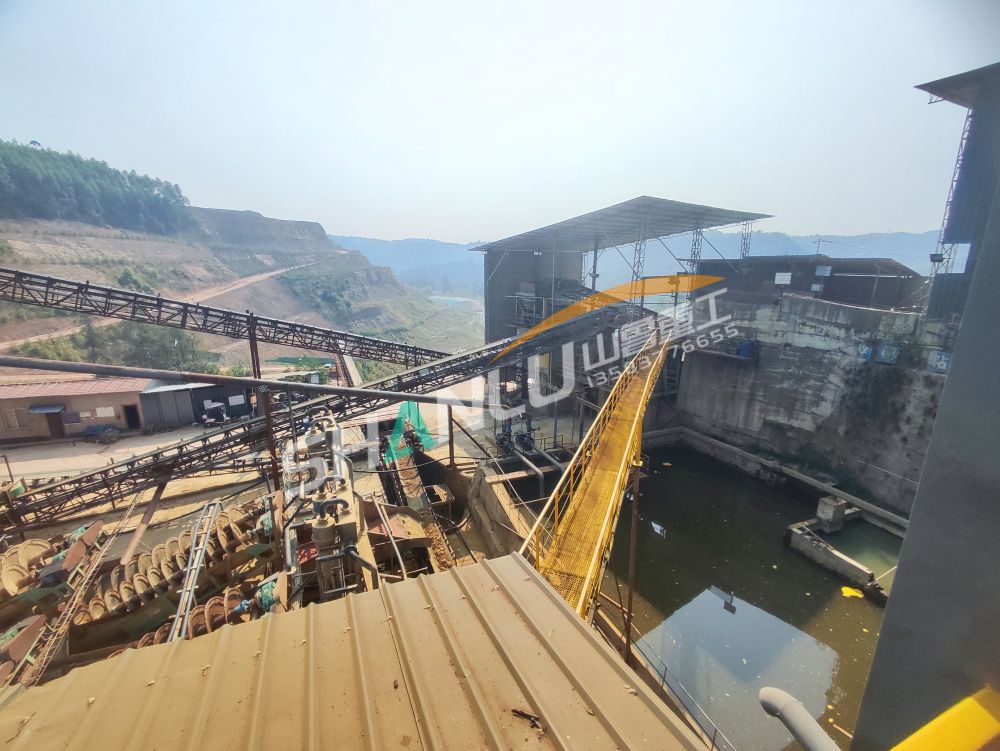
1. Pool structure design
Tank size and capacity: Based on the demand for production and wastewater
volume, the capacity of the sedimentation tank should be large enough to ensure
sufficient sedimentation time and separation effect. Usually, the depth of the
pool should not be less than 2 meters, and the width and length should be
reasonably configured according to the processing capacity of the washing
equipment.
Pool wall design: The pool wall should be smooth, sturdy, avoid mud adhesion,
and consider anti-corrosion design. Concrete, steel plates and other materials
can be used, and anti-corrosion coatings can be applied to enhance
durability.
Bottom design: The bottom of the pool should have an appropriate inclination
(usually 1% to 2%) to facilitate the sedimentation of mud into the mud
collection area at the bottom of the pool. A mud discharge outlet should be
installed at the bottom to facilitate the discharge of deposited mud.
2. Control of sewage flow rate and velocity
Water flow velocity design: The design of the sedimentation tank should
ensure a moderate water flow velocity to avoid water flowing too fast and
affecting the sedimentation effect. Generally, it is required that the speed of
water flow should be below 0.5 m/s to avoid disturbing the sediment layer.
Inlet and outlet design: The wastewater inlet should avoid direct violent
impact on the water in the pool, and is generally designed as a laminar or
transverse inlet. The outlet position of the sedimentation tank should be
designed reasonably to ensure that the settled mud is not carried away and that
the sewage is effectively discharged.
3. Sedimentation area and sludge discharge area
Sedimentation zone: When designing a sedimentation tank, the physical process
of sedimentation must be considered to ensure that the wastewater has sufficient
time to settle after entering the tank. A certain sedimentation area should be
set up at the bottom of the sedimentation zone to fully meet the sedimentation
needs of the mud.
Mud discharge area: The sedimentation tank should be equipped with a mud
discharge system, which is generally designed at the bottom of the tank or on
one side of the bottom. Mud is automatically discharged through the mud
discharge pipeline, reducing the frequency of manual cleaning.
4. Mud collection device
Mud collection tank and pumping device: A mud collection tank is installed at
the bottom of the sedimentation tank to collect the settled mud. An automatic
mud extraction system can be designed, such as using scraper plates, screw
conveyors, etc., to regularly extract the accumulated mud at the bottom of the
pool, avoiding insufficient pool volume caused by excessive mud.
Mud concentration: When collecting mud, a mud concentration device can be
designed to further increase the solid content of the mud through chemical
treatment or sedimentation, thereby reducing wastewater discharge.
5. Clean water recovery system
Water reflux design: The clear water in the sedimentation tank flows back to
the washing equipment through the overflow port for secondary utilization, which
can reduce the use of external water sources and lower water treatment costs.
The clear water reflux system should be equipped with a filtering device to
remove fine particles that may be carried out.
6. Anti corrosion and anti leakage design
Anti corrosion design of the tank body: Due to the long-term immersion of
highly acidic and corrosive sewage in the sedimentation tank, the tank body and
pipeline system must be treated with anti-corrosion measures. Common
anti-corrosion materials include anti-corrosion coatings, stainless steel,
fiberglass, etc.
Leakage protection: The bottom and walls of the pool need to be designed with
anti leakage measures to prevent wastewater from leaking into groundwater or the
environment. Polyethylene film, anti leakage coating and other methods can be
used for treatment.
7. Sewage treatment and reuse
Wastewater sedimentation post-treatment: The clear water in the sedimentation
tank can be used in the reflux water washing system through post-treatment
processes such as filtration and disinfection. If the water pollution is severe,
further treatment can be considered, such as using ultrafiltration, reverse
osmosis and other technologies to improve water quality and meet reuse
standards.
Waste mud treatment: The mud in the sedimentation tank needs to be centrally
treated. If the mud contains harmful substances, it should be safely treated in
accordance with environmental protection requirements to avoid polluting the
environment.
8. Monitoring and automation control
Water level and flow monitoring: Water level gauges and flow meters should be
installed to monitor the water level and flow rate in the sedimentation tank in
real time, to prevent overflow or excessive water flow from affecting the
sedimentation effect.
Automatic cleaning system: Consider configuring an automatic cleaning system
to clean up the accumulated sludge or sediment in the sedimentation tank and
improve its efficiency.
summarize
The design of the mud sedimentation tank for quartz sand washing equipment
not only needs to consider the stability and durability of the structure, but
also pays attention to the treatment of wastewater and the reuse of water
resources. Good design can effectively improve sedimentation efficiency, reduce
environmental risks, and lower operating costs. Through precise water flow
control, mud collection, wastewater recovery and other measures, efficient
management and treatment of wastewater in the quartz sand production process can
be achieved.