Standard for setting temperature control parameters of quartz sand
calcination kiln
The quartz sand calcination kiln removes impurities (such as organic matter,
iron, etc.) from quartz sand through high-temperature treatment to improve its
purity, especially in the production of high-purity quartz sand. The key to this
process lies in precise temperature control, as temperatures that are too high
or too low may affect the calcination effect and product quality. The following
are some basic setting standards and parameters for temperature control of
quartz sand calcination kiln.
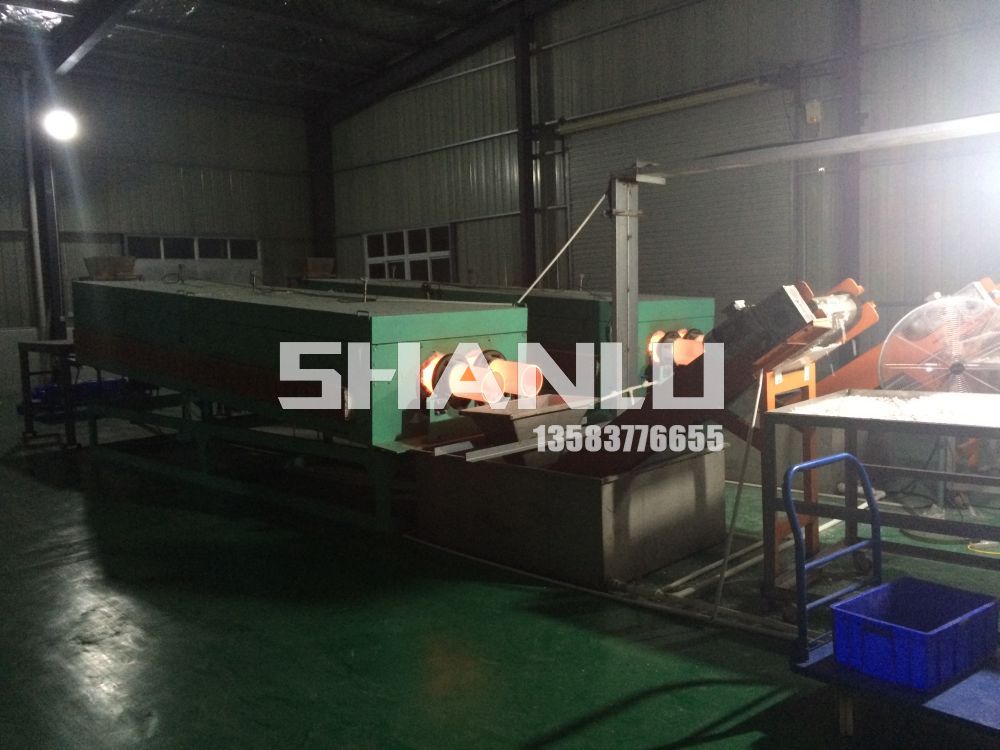
1. Calcination temperature range
Conventional calcination temperature for quartz sand: Generally, the
calcination temperature for quartz sand is set within the range of 1000 ℃ to
1200 ℃. This temperature range is sufficient to remove organic impurities
without excessive melting or damaging the crystal structure of quartz sand.
Calcination temperature of high-purity quartz sand: For the production of
high-purity quartz sand, more precise control is usually required, and the
temperature range can be set between 1100 ℃ and 1300 ℃ to ensure the maximum
removal of impurities such as iron, aluminum, and titanium and improve
purity.
Mineral composition influence: Impurities in quartz sand, such as iron
minerals, bauxite, clay, etc., can affect the setting of calcination
temperature. For quartz sand containing more iron, higher temperatures may be
required to effectively remove it.
2. Temperature control parameters
Heating rate: The heating rate has a significant impact on the calcination
effect. If the temperature is raised too quickly, it may cause cracks or
overheating on the surface of quartz sand, so the heating should be slow. The
general heating rate is controlled between 50 ℃/h and 100 ℃/h.
Insulation time: The insulation time during the calcination process depends
on the particle size, impurity content, and required calcination effect of the
quartz sand. In general, the insulation time should be maintained between 2 to 5
hours to ensure uniform temperature distribution and sufficient removal of
impurities. For larger grained quartz sand, a longer insulation time may be
required.
Cooling rate: The cooling rate also affects the properties of quartz sand.
Rapid cooling may cause changes in the crystal structure of quartz sand,
affecting its physical properties. Therefore, the cooling rate should usually be
controlled between 50 ℃/h and 100 ℃/h, and slow cooling can ensure that the
quality of quartz sand is not affected.
3. Temperature distribution and control
Uniformity of temperature distribution inside the kiln: During the
calcination process, the uniformity of temperature distribution inside the kiln
is very important. The temperature should be kept stable to avoid local
overheating or overcooling. The temperature uniformity inside the kiln can be
ensured through reasonable air flow and heat exchange design.
Temperature sensors and automation control: To ensure the accuracy of
temperature control, high-precision temperature sensors (such as thermocouples)
and automated temperature control systems should be used for real-time
monitoring and adjustment. The temperature control system should be able to
automatically adjust the combustion state and air volume of the burner according
to the temperature changes in different areas of the kiln.
Multiple temperature control zones: In some large calcination kilns, multiple
temperature control zones may be set up, with each zone independently
controlling the temperature. For example, the front section of the kiln can be
preheated at a lower temperature (about 1000 ℃), while the rear section of the
kiln uses a higher temperature for main calcination.
4. Combustion system and atmosphere control
Combustion gas selection: Common combustion gases include natural gas, coal
gas, liquefied petroleum gas, etc. Different fuels have different effects on
temperature, and controlling gas flow rate and burner position is crucial to
ensure uniform temperature inside the kiln.
Oxygen supply and atmosphere regulation: During the calcination process of
quartz sand, it is necessary to control the oxygen concentration inside the kiln
to ensure sufficient combustion. The supply of air and atmosphere inside the
kiln also need to be adjusted to avoid the formation of a reducing atmosphere or
an excessive oxidizing atmosphere, which may affect the effectiveness of
impurity removal.
5. Temperature monitoring and adjustment inside the kiln
Real time temperature monitoring: By installing temperature sensors and
combining them with an automatic control system, it is possible to monitor
temperature changes inside the kiln in real time. Common temperature sensors
include thermocouples and infrared temperature sensors.
Automatic temperature adjustment: When the temperature fluctuation exceeds
the set range, the automation system can adjust the temperature by adjusting the
fuel supply or gas flow rate to ensure stable temperature inside the kiln.
6. Quality control and monitoring
Sample analysis: Regularly sample and analyze the chemical composition of
quartz sand to ensure its purity and whiteness meet the standards. If the iron
content of quartz sand is too high or the whiteness is not enough, it can be
optimized by adjusting the temperature parameters.
Finished product inspection: The calcined quartz sand needs to undergo
particle size analysis, purity testing (such as iron content detection), and
whiteness testing to ensure that the final product meets industry
requirements.
summarize
The temperature control of quartz sand calcination kiln is crucial for
improving the purity, whiteness, and final product quality of quartz sand. By
accurately setting the temperature range (1000 ℃ to 1300 ℃), controlling the
heating rate, insulation time, and cooling rate reasonably, and ensuring uniform
temperature distribution inside the kiln, the calcination effect of quartz sand
can be effectively improved. Meanwhile, adopting an automated control system for
real-time monitoring and adjustment of temperature is the key to improving
production efficiency and product consistency.