High purity horizontal sand making machine is a fine crushing equipment
designed specifically for the processing of high-end non-metallic minerals such
as high-purity quartz sand. It is widely used in high-tech industries such as
electronics, photovoltaics, optical fibers, semiconductors, and aerospace for
the precise preparation of high-purity quartz raw materials. It has an
irreplaceable position in the high-end sand making field due to its advantages
of horizontal structure design, low iron pollution control, high efficiency
crushing, and high degree of automation.
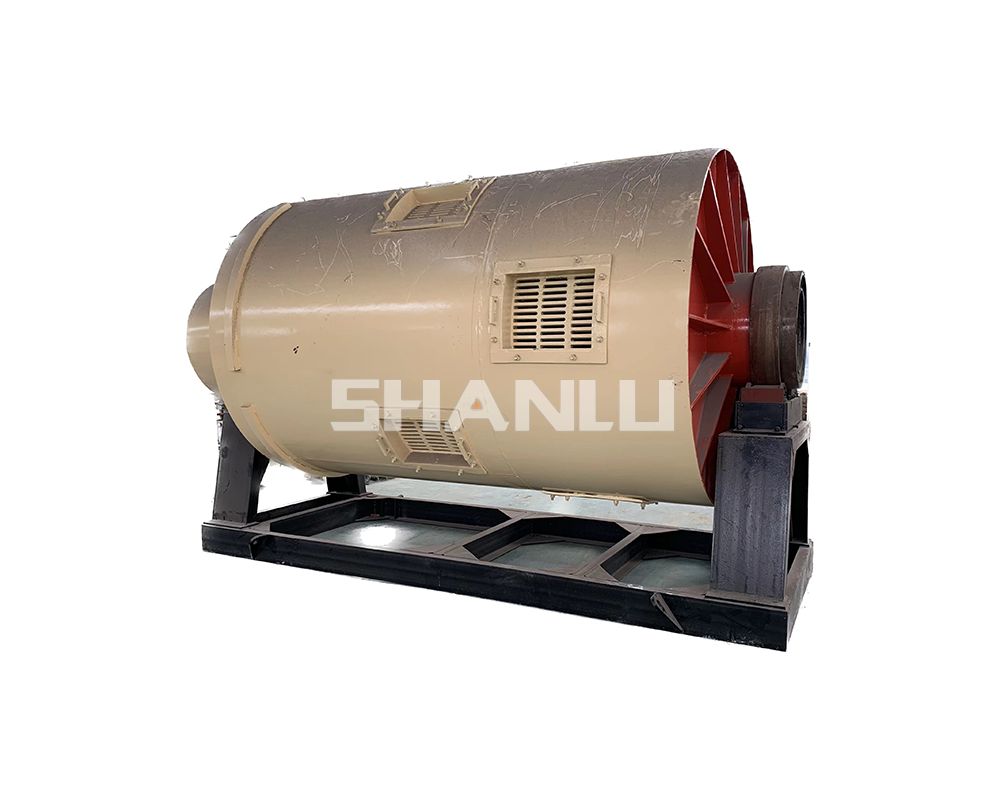
From the perspective of equipment structure, high-purity horizontal sand
making machines adopt a horizontal layout, where the main shaft is placed
horizontally and the internal rotor or hammer rotates at high speed in the
horizontal direction. This structure is conducive to uniform feeding and
continuous processing of materials, and can effectively avoid non-uniform impact
caused by the self weight of materials falling during vertical sand making
process, thereby achieving more accurate and uniform crushing effect. At the
same time, the horizontal design is also convenient for equipment maintenance
and cleaning, especially suitable for high-purity material fields that require
extremely high production cleanliness and equipment pollution-free
requirements.
In terms of core functions, the high-purity horizontal sand making machine
uses a high-speed rotor to throw out the material at high speed, and collides
and crushes it with the high hardness lining plate, other materials or ceramic
layers in the crushing chamber. To ensure the purity of the product, the
equipment usually uses high-purity ceramics, zirconia, stainless steel, or
special alloy materials to manufacture the rotor, lining plate, and casing,
effectively controlling the precipitation of metal impurities and minimizing the
pollution of iron, aluminum, copper and other elements on the purity of the
finished product. This high standard material selection and special structural
design enable high-purity horizontal sand making machines to maintain extremely
low levels of metal contamination when processing high-purity quartz sand,
ensuring that the final product can be used for high-precision applications at
the semiconductor level.
In addition, in order to meet the stringent requirements of modern
high-purity material processing, this type of sand making machine is usually
equipped with efficient dust removal devices and fully enclosed structures,
which can effectively reduce dust leakage during the production process,
maintain a clean production environment, and keep the workshop pollution-free.
In terms of airtight design, most high-purity horizontal sand making machines
adopt multiple sealing devices, such as mechanical seals, wind pressure seals,
or water seal systems, to ensure that dust does not leak out and impurities do
not enter, improve the cleanliness level of the sand making environment, and
comply with GMP or clean room standards.
In terms of operational efficiency, high-purity horizontal sand making
machines have advantages such as controllable discharge particle size,
concentrated fineness distribution, and regular finished product particle size.
By adjusting the rotor speed, discharge gap, feed rate, and screening system,
precise control of the particle size of the finished product can be achieved,
meeting the technical specifications of various high-purity material particle
size distributions. Some devices also integrate intelligent control systems,
which can achieve functions such as automatic start stop, remote monitoring,
fault alarm, and production statistics, greatly improving the automation level
and management efficiency of the entire sand production line.
From an application perspective, high-purity horizontal sand making machines
have a wide range of applications in the field of high-end quartz material
processing. For example, in the preparation process of high-purity quartz sand,
natural quartz or primary purified quartz coarse materials need to be further
finely divided into fine particles with uniform particle size distribution and
extremely low impurity content, which can be used as precursors for raw
materials such as photovoltaic glass, quartz crucibles, and optical fiber rods.
Traditional sand making equipment cannot meet this purity requirement due to the
large number of metal components and high pollution of wear-resistant materials.
However, high-purity horizontal sand making machines, with their special
material and structural design advantages, can stably output high-quality
fine-grained quartz sand, becoming the preferred equipment for deep processing
of high-end quartz sand.
In order to further optimize equipment performance, high-purity horizontal
sand making machines can also be equipped with high-precision classification
equipment, such as airflow classifiers, centrifugal classifiers, or multi-layer
vibrating screens, to classify finished particles and achieve multiple controls
on particle size, purity, and particle shape. In addition, in some application
scenarios where particle size requirements are extremely strict, this equipment
can also operate in conjunction with ultrafine mills to achieve secondary or
multi-stage refinement processes, thereby meeting higher-level precision
machining needs.
In summary, the high-purity horizontal sand making machine is a professional
sand making equipment designed specifically for high-end quartz sand and other
high-purity non-metallic mineral processing scenarios. It integrates low
pollution, high efficiency, high automation, and stable operation, and is a key
equipment for achieving high-quality raw material supply in industries such as
photovoltaics, semiconductors, and new materials. With the continuous growth of
global demand for high-end raw materials such as high-purity quartz sand, and
the deepening promotion of green, environmentally friendly, and intelligent
manufacturing concepts, high-purity horizontal sand making machines will play an
increasingly important role in the field of material deep processing in the
future, and continue to lead the development direction of sand making equipment
technology.