In the field of quartz sand deep processing, whether used for photovoltaic
glass, semiconductor substrates, high-end ceramics, or precision casting, there
are almost strict requirements for the particle size distribution, purity, and
particle morphology of quartz sand. How to efficiently and stably convert raw
quartz ore into high-quality powder that meets standards? The quartz sand
special ball mill is an indispensable professional equipment for this core link.
With its unique design and craftsmanship, it has become the key to breaking
through the bottleneck of quartz sand processing and enhancing product value.
This article will provide a detailed analysis of its working principle, core
advantages, and selection points, providing practical guidance for improving the
quality and efficiency of your quartz sand.
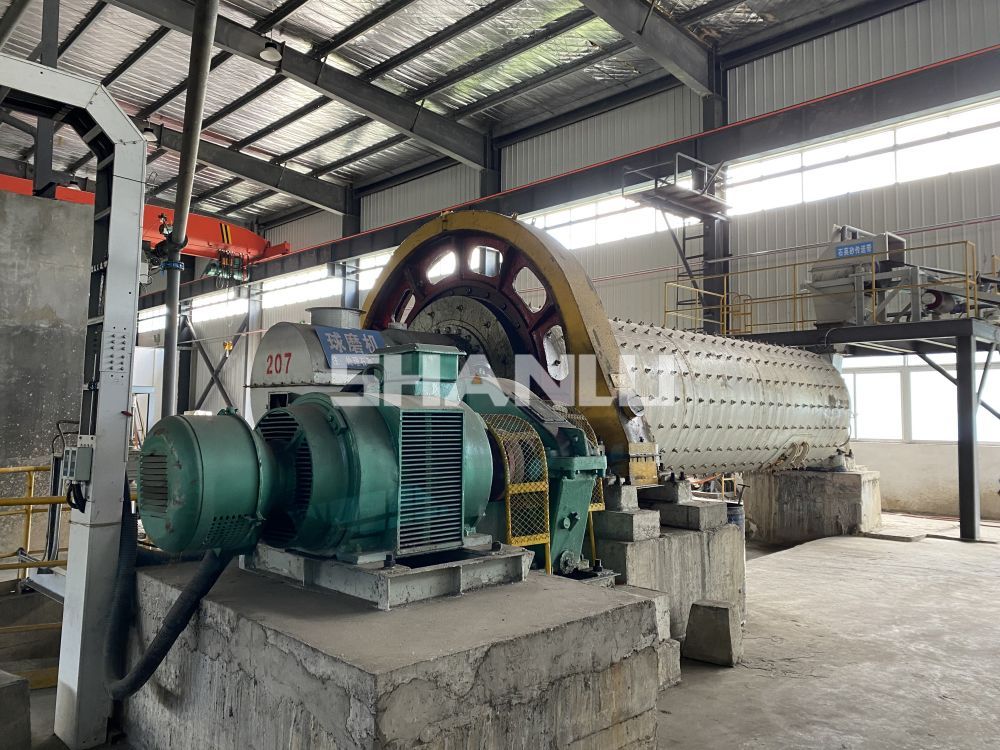
1、 The core challenge of quartz sand processing and the key role of ball
mills
In the process of quartz sand processing, there are generally three core pain
points:
Strict purity requirements: It is necessary to strictly avoid contamination
by impurities such as iron to ensure a high SiO2 content in the final product,
which is crucial for high-end applications such as photovoltaics and
semiconductors.
Accurate particle size control: Different application scenarios (such as
photovoltaic sand, casting sand, filler sand) have specific and strict standards
for the particle size distribution (such as D50, D97) of quartz sand.
Balancing high energy consumption and efficiency: Grinding is one of the most
energy consuming processes in quartz sand processing, and how to effectively
control costs while ensuring efficiency is the key.
A professional quartz sand ball mill, with its flexible and controllable
grinding method (dry or wet method can be selected), excellent grinding
efficiency, and effective control of pollution risks (such as using non-metallic
materials such as ceramic lining plates and quartz stone lining plates), has
become the ideal choice to solve these pain points and is the core equipment to
ensure the quality and production efficiency of quartz sand.
2、 Professional customized design of quartz sand ball mill
Unlike conventional ball mills, quartz sand ball mills have undergone
multiple key optimizations based on the characteristics of quartz sand to ensure
efficient and pure grinding results
Core structure optimization:
Grinding core: The core of the equipment is the rotary cylinder, which is
loaded with grinding media of specific proportions and materials (such as high
alumina ceramic balls, silica balls, natural pebbles) and quartz sand raw
materials.
Precise power drive: The motor precisely controls the rotational speed of the
cylinder through a reducer (usually set at 60% -75% of the critical speed),
producing the best impact and grinding effect for the grinding medium.
The essential lining: high-purity wear-resistant non-metallic lining plates
(such as high alumina ceramics, silica, rubber, or polyurethane) are the soul of
quartz sand ball mills. It minimizes metal pollution such as iron to the
greatest extent possible, ensuring high purity of quartz sand products, while
also possessing excellent wear resistance, extending the service life of
equipment.
Efficient feeding and discharging system: The optimized feeding device
ensures smooth material entry, while the discharge design ensures that the
target particle size requirements are met. It is usually used in conjunction
with classification equipment such as air separators and hydrocyclones.
Scientific selection of grinding media:
Strict material requirements: Iron containing media must be completely
avoided. Common choices include high alumina ceramic balls, natural pebbles,
silica balls, etc. The choice of material directly affects the purity and
grinding efficiency of the product.
Accurate grading scheme: The size ratio (grading) of the grinding medium is
the key to controlling the grinding efficiency and final product particle size
distribution. Scientific design is required based on the hardness, initial
particle size, and target fineness of quartz sand.
Flexible and adaptable grinding process:
Advantages of wet grinding: adding water or specific grinding aids for
grinding. This method is usually more efficient, can effectively reduce dust,
and is easier to obtain ultrafine quartz powder (such as for electronic grade
silicon micro powder), but it requires additional dehydration and drying
processes in the future.
Characteristics of dry grinding: Grinding directly in an air environment. The
process flow is relatively simple and suitable for applications that are
sensitive to moisture or do not require ultrafine powder standards (such as some
casting sands and filter media), but require an efficient dust removal system to
control dust.
3、 The core advantages of choosing a quartz sand specific ball mill
Investing in professional quartz sand ball mills can bring significant value
to your production:
Purity assurance expert: The application of non-metallic lining and grinding
media eliminates the risk of iron pollution from the source, ensuring that
quartz sand products maintain extremely high SiO2 purity and easily meet the
strict quality requirements of high-end industries such as photovoltaics and
semiconductors.
Accurate control of particle size: By flexibly adjusting core parameters such
as the grading of the grinding medium, cylinder speed, and grinding time, the
particle size distribution of the final product (such as D50, D97) can be
accurately controlled, and it can flexibly adapt to different specifications and
standards for downstream applications.
Efficient and energy-saving model: Optimized equipment structure design (such
as efficient transmission system, lining plate shape to reduce energy
consumption) and reasonable process parameter settings significantly reduce
energy consumption per unit product, directly improving production economic
benefits.
Stable operation guarantee: Based on mature and reliable structure,
wear-resistant design of key components, and high-quality manufacturing, the
quartz sand ball mill can ensure long-term continuous and stable production
operation, effectively reducing maintenance costs and losses caused by
unexpected shutdowns.
Wide adaptability to raw materials: It has good tolerance for particle size
fluctuations of quartz sand raw materials and a wide range of processing
capabilities. Suitable equipment models can be found for both small-scale
experimental lines and large-scale industrial production lines.
4、 Key Selection and Application Technical Parameters Reference
When choosing a quartz sand ball mill, it is important to pay attention to
the following technical parameters and match them according to actual needs:
Processing capacity: Wide range, ranging from 0.5 tons per hour to over 100
tons per hour, depending on the scale of your production line.
Cylinder size: Diameter and length (such as Ø 900x1800mm to Ø 3600x850mm or
larger) directly affect equipment capacity and required installation space.
Drive power: typically ranging from 18.5 kW to over 1000 kW, depending on
cylinder size, material loading capacity, and target grinding fineness.
Working method: Based on the final product requirements and subsequent
processes, determine whether to choose dry grinding or wet grinding.
Lining material: High alumina ceramics, silica, rubber, and polyurethane are
the core choices for quartz sand ball mills, which must ensure non-metallic,
high wear resistance, and extremely low introduction of impurities.
Grinding media: Ceramic balls, pebbles, and silica balls are the mainstream
choices, and the specific material, size, and grading scheme need to be
precisely designed according to the fineness of the target product.
Feed particle size: It is usually required to be less than 20 millimeters.
Excessive raw material particles can significantly affect grinding efficiency
and require pre-treatment with pre crushing equipment.
Discharge particle size: The target fineness (commonly represented by D97)
has a wide range, such as 45 microns (about 325 mesh) to 10 microns (about 1250
mesh) or finer, which directly determines the required grinding time and the
choice of grinding medium.
Working speed: usually set between 60% and 75% of the critical speed, this
parameter affects the mode of action of the grinding medium (mainly impact or
grinding) and overall efficiency.
Classification matching: Classification equipment such as air separators,
hydrocyclones, or vibrating screens are crucial as they can effectively separate
qualified particle size products, improve the overall efficiency and control
accuracy of the grinding system.
5、 Successful application case: Professional ball mill drives value leap
Case 1: Photovoltaic Glass Sand Enterprise - This enterprise adopts a large
wet process ceramic lined quartz sand ball mill and is equipped with a hydraulic
cyclone group for precision grading. Successfully processed the raw materials
into D50 stable at 35 ± 2 microns, strictly controlling the content of large
particles larger than 75 microns, and reducing the increase in iron impurities
to less than 50ppm. This not only significantly improves the transmittance of
photovoltaic glass products, but also greatly increases the production
yield.
Case 2: High end precision casting quartz powder production - using dry
silica lining plate quartz sand ball mill, combined with efficient dynamic air
sorting machine. Stable production of low sodium and low impurity quartz powder
with D97 ≤ 45 microns (325 mesh). The product perfectly meets the demanding
requirements of high temperature stability and detail reduction of molding sand
for complex castings, helping customers achieve significant product premium.
Case 3: Preparation of Electronic Grade Silicon Micro Powder - Multiple small
high-purity ceramic lined quartz sand ball mills are used for series ultrafine
grinding, and strict iron removal processes are implemented, combined with
precision grading technology. Finally, we successfully obtained ultrafine
high-purity silicon micro powder with D50 ≤ 5 microns (SiO2 content>99.99%)
and successfully entered the supply chain of high-end copper-clad laminates and
chip packaging materials.
6、 Professional selection and optimization suggestions
To ensure maximum return on your investment, please follow the following
recommendations:
Clear definition of core requirements: Firstly, clarify the granularity (D50,
D97), purity requirements (especially iron content), required production
capacity, and project budget of the target product.
In depth assessment of supplier strength: Focus on evaluating the supplier's
professionalism in material purity and wear-resistant solutions for lining
plates and grinding media, equipment processing accuracy (affecting sealing and
pollution control), and whether there are successful cases of handling similar
quartz sands.
Strive for material sample verification: Provide your quartz sand raw
materials for small-scale or pilot tests as much as possible, and run them on
the equipment to verify the grinding effect and whether various parameters meet
the standards.
Consider intelligent upgrading: Evaluate the feasibility of integrating
online granularity monitoring instruments, automatic control systems, and other
intelligent supporting systems to improve production stability and efficiency,
and reduce manual intervention.
Focusing on the full lifecycle cost: The selection decision should not only
consider the initial purchase price of the equipment, but also take into account
the total cost of the entire lifecycle, including energy consumption, grinding
medium consumption, maintenance costs, and potential downtime losses.
conclusion
The quartz sand ball mill is not a simple crushing tool. It is a specialized
precision equipment that safeguards the purity lifeline of quartz sand products,
accurately shapes particle size and shape, and achieves efficient and
energy-saving production. In today's increasingly high-end development of quartz
sand applications, investing in a professional quartz sand ball mill with
scientifically designed, high-quality materials, and process matching is a
strategic decision to connect the core links of high-quality quartz sand
production, significantly enhance product market competitiveness and added
value.
Consult professional quartz sand ball mill solutions immediately for
customized selection suggestions and exclusive quotes, allowing you to grind
high-purity quartz sand in one step! Embark on a new chapter of efficient and
high-quality production, starting with a professional choice.